How Apex Competes in a Fragmented Packaging Industry
The blow-molded bottles and packaging containers industry is highly competitive and fragmented. At Apex Plastics, we survive and thrive in this demanding marketplace through our most important strategy: specialization.
Apex’s success hinges on producing high-quality packaging and outstanding customer service for clients and prospects that need small- and medium-sized production runs. Apex also differentiates itself from competitors through our expertise in specialty colors and weights and producing customized shapes and containers that meet our customers’ unique packaging requirements.
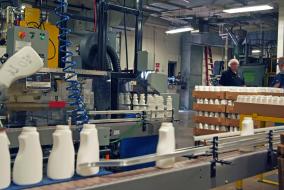
Our industry is driven by geography. The cost to ship products can make or break a business deal, so Apex finds it advantageous to gain business and build solid relationships with customers within 500 miles of our headquarters and plant in Brookfield, Missouri.
“We want to saturate a 500-mile radius to capture more business,” says operations manager Nick Hansen. “Our recently expanded production capacity means we can capture more mid-sized production business that we weren’t able to get until now.”
Apex offers customers other advantages many competitors can’t match:
Excellent customer service with short turnaround times. Even when Apex can’t beat others on price, we still win new business and maintain customers because outstanding Apex employees provide better customer service and faster production than competitors.
ISO certified and FDA registered
All Apex products are certified and fully comply with processes and procedures outlined in ISO (International Organization for Standardization) standards. Apex also is registered with the U.S. Food and Drug Administration, which ensures our products meet or exceed federal safety standards. These assurances of quality and safety are not met by all packaging operations.
Commitment to growth
Apex stays on the leading edge of the packaging industry by expanding and innovating to stay ahead of customer demand. We have added one blow molding press and plan to add a second (see additional article in this newsletter for details). Plus, we are upgrading our headquarters; adding manufacturing space, and adding warehouse space and a new office.
The Apex team’s willingness to go the extra mile for customers, Hansen says, is one of the most critical elements helping the company survive and thrive in the packaging industry. “You become willing to try anything your customers want to go for,” he said. “If they bring a new project to you, you don’t say no often, even if you can’t say yes to everything. It’s important for Apex to remain competitive with every job.”